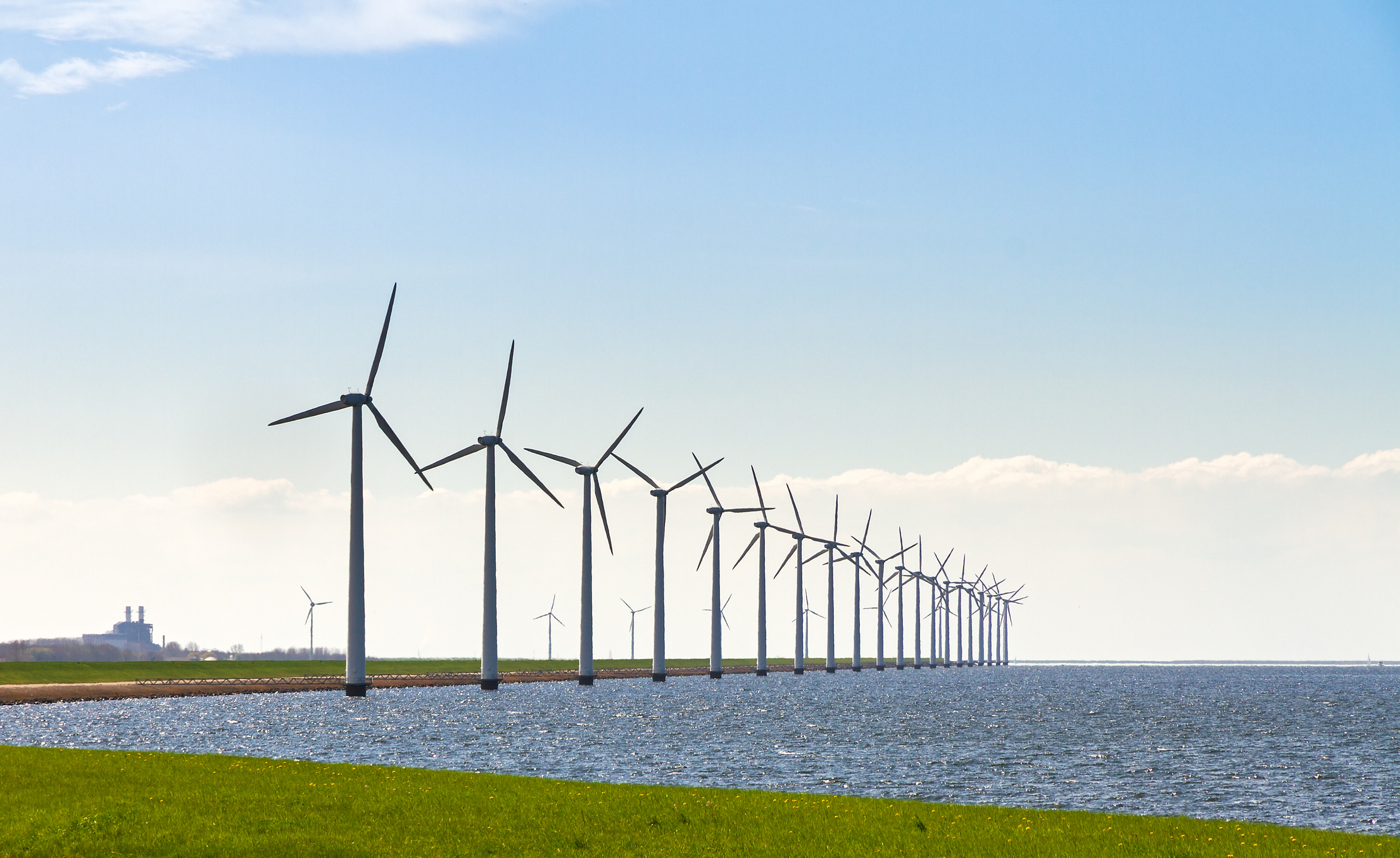
Don Quijote alakja az örök illúziók és reménytelen küzdelmek (szélmalomharcok) allegóriája lett. De mi a helyzet a karbantartással? Tényleg el kell fogadnunk, hogy visszatérő problémák közt élünk és a megbízható eszközpark csak egy délibáb a távolban, amit mindhiába kergetünk?
Mi az oka annak, hogy egy helyben toporgunk?
- Nem érünk rá, tüzet kell oltani! Ha a szervezet géphibától géphibáig él és rohan, túlterhelt és stresszes, akkor bizony nehéz megállni és higgadtan előre gondolkozni. Örülünk, ha a napot túléljük és a munkaidő vége után néhány órával hazamehetünk, megússzuk a hétvégi és esti telefonokat.
- Nem marad elegendő gyártókapacitás a vevők kiszolgálására! A géphibák és a kiszámíthatatlan működés lehetetlenné teszi a határidőre való szállítást. Ennek eredményeképp a karbantartás még inkább a tűzoltásra fókuszál, nem marad idő a tervezett karbantartások elvégzésére sem. A negatív spirál tovább erősödik.
- További – a negatív spirált erősítő – jellemző jegy, hogy az időhiány, kényszer szülte megoldásokat eredményez (szaknyelven: sufni tuning), melyeknek a know-how-ja csak annál elérhető, aki elkövette. Nem tudjuk a miértet és a hogyant, ráadásul újabb hibákhoz vezethet.
- Nem látható a probléma! Habár a szervezet érzi, hogy a gépek működése nem kellően megbízható, de ez inkább „csak egy vélemény”. Nem állnak rendelkezésre a megfelelő adatgyűjtő rendszerek. A hibák bejelentése telefonon, esetleg e-mailben történik, nem is beszélve a termelés szintjén elhárított problémákról. A visszakereshetőség és a leggyakoribb hibák azonosítása legfeljebb komoly erőfeszítések árán érhető el.
- A strukturált problémamegoldás hiánya! Ha el is jutunk egy-egy visszatérő probléma felismeréséig, nem fordítunk kellő hangsúlyt a kiváltó okok megértésére és kezelésére. „Csípőből tüzelünk”, olyan akciókat határozunk meg, amelyek nem feltétlen kezelik a bekövetkezett probléma kiváltó okait, már ha egyáltalán eljutunk a megvalósításig.
Mit nyerhetünk a visszatérő problémák tudatos azonosításával és kezelésével?
- Javul a munkabiztonság a gépek állapotának javulásával
- Jobb a vevőkiszolgálás
- Stabilitás és tervezhetőség: kevesebb váratlan esemény zavarja meg a termelési terv teljesülését, amelynek eredményeként kevesebb utólagos beavatkozás szükséges.
- Rugalmasság: a váratlan hibák miatt kieső idő csökkenésével a felszabadult kapacitás egy része átállásokra, így a vevői igények változásának gyorsabb követésére, vagy a készletszintek csökkentésére fordítható.
- Kiszámítható munkavégzés az emberek szintjén, kevesebb stressz, idegesség, túlóra és váratlan helyzet.
- Javuló gépi rendelkezésreállás, amely komolyabb beruházás nélkül is többlet kapacitást jelent a gyártás számára.
- Csökkenő alkatrészfelhasználási költség – „miért cserélünk havonta csapágyat?”
- Idő szabadul fel, amelyet megelőzésre fordíthatunk!
- Dolgozói elégedettség
Hogyan szoríthatjuk vissza a tűzoltás mértékét?
- Törjünk ki a negatív spirálból akár plusz erőforrások bevonásán keresztül (pl. kezdeti tisztítások megkezdése, megelőző karbantartások rendszeres elvégzése, hibaelőjelek elhárítása) és fejlesszük a karbantartás működését! A már ott dolgozók mélyebb bevonása a napi karbantartásba, ellenőrzésbe, tisztításba nem is feltétlenül plusz erőforrás, hanem helyesen már ott lévő erőforrás felhasználása.
- A rendelkezésre álló erőforrások felhasználása során priorizáljunk, kockázatértékelés alapon határozzunk a súlypontokról és a legkritikusabb problémákról!
- Tudatosan keressük a meghibásodások előjeleit és kezeljük azokat!
- Vezessük be a TPM rendszert, hogy plusz kapacitást nyerjünk a gyártás számára. Nem csak a géphibák kezelésével szabadíthatunk fel időt. Csökkentsük az átállások hosszát, a mikroleállások miatt kieső időt és más egyéb a gépekhez kötődő veszteségforrásainkat is.
- Fejlesszük a szervezeti egységek közötti együttműködést és kommunikációt! A problémák rendszeres megosztása, a feladatkörök és kölcsönös elvárások tisztázása és így az együttműködés erősítése nem kerül pénzbe a vállalat számára, még is jelentős növekedés jelenthet a hatékonyság terén!
- Fejlesszük adatgyűjtő rendszereinket! Amit nem mérünk, azt megfelelően kezelni sem tudjuk! Törekedjünk a géphibák visszakövethető dokumentálására és az állásidők, valamint a kapcsolódó mérföldkövek (pl. géphiba időpontja, karbantartó kiérkezése a géphez, elhárítás időpontja, termelés indulása stb.) valós mérésére!
- Priorizáljuk a mérések alapján felszínre került problémákat! Oda helyezzük a fókuszt, ahol a legnagyobb hatást érhetjük el!
- Tudatosan elemezzük és kezeljük a felszínre került problémákat a PDCA logikának megfelelően, strukturált probléma megoldó módszerek segítségével! Fejlesszük embereink problémamegoldó képességét!
- Vonjunk be külső szakértőket! Ha úgy érezzük, hogy a problémák túlnőttek rajtunk vagy túl bonyolultak, ne habozzunk! Nem szégyen külső erőforrást bevonni akár tudás, akár kapacitás szempontból sem!
Ön is tudja, hogy a visszatérő műszaki problémák megelőzése időt és erőforrásokat takarít meg a szervezetnek, mivel nem kell folyamatosan azokkal foglalkozni.
Emellett javítja a munkahelyi hatékonyságot és a dolgozók morálját, mivel a stabil műszaki környezet kevesebb stresszt és frusztrációt okoz.
GYORSFÉNYKÉP
3 perc
e-mail
Átfogó képet kap arról, mekkora erőforrást szabadíthat fel a vállalatánál
KONZULTÁCIÓ
60 perc
online
Testreszabott szakértői támogatás a vezetői kihívásai alapján megfogalmazott kérdésekben
GYAKORLATI TECHNIKÁK
1 nap
személyes
Bevezető tréning a megvalósítás módszereibe: Hogyan szabadíthatja fel a rejtett tartalékokat a vállalatánál?